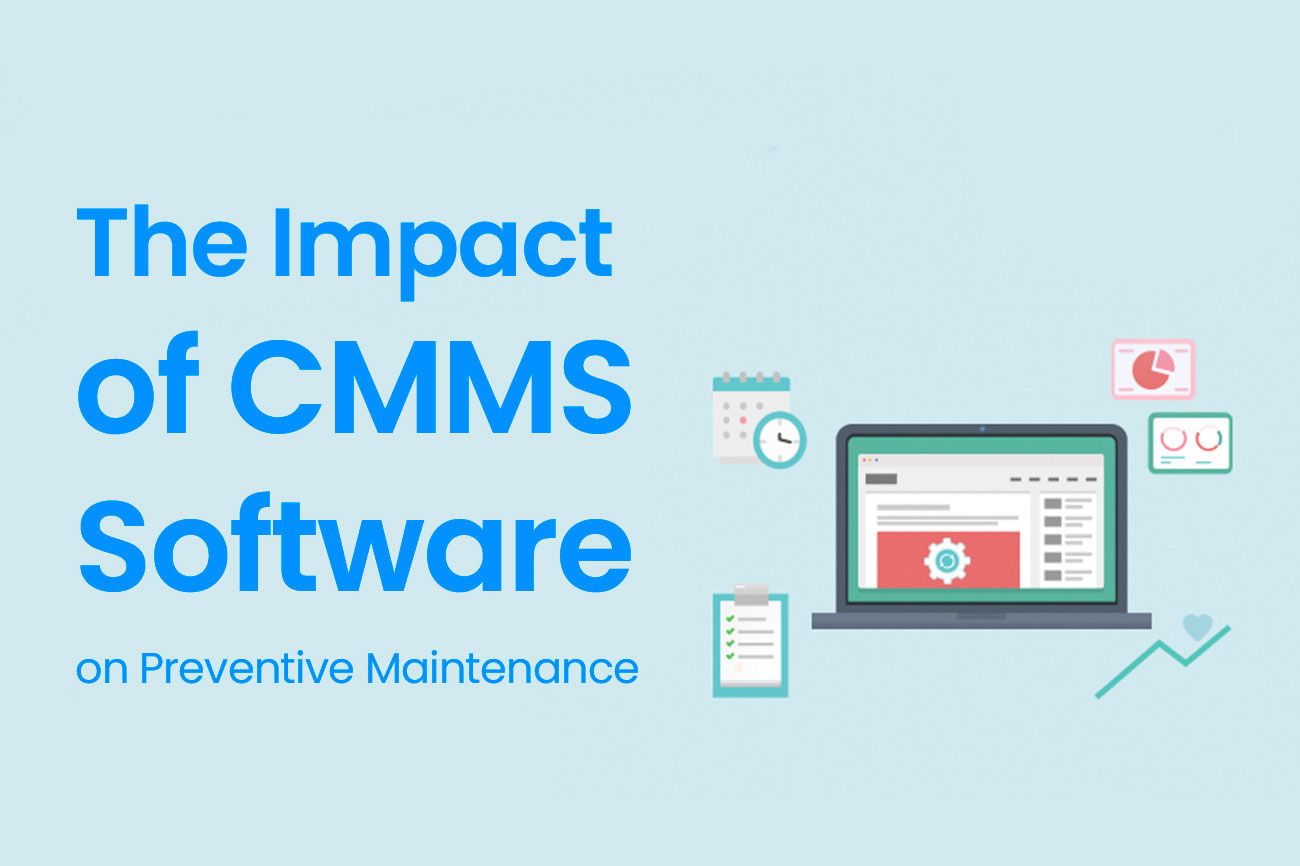
The Impact of CMMS Software on Preventive Maintenance
Maintaining seamless functionality of machinery and equipment is essential in the dynamic landscape of industrial operations. A sudden breakdown can disrupt production, incur significant financial losses, and tarnish a company's reputation. This underscores the importance of preventive maintenance as a proactive measure to avert such costly disruptions.
However, managing preventive maintenance schedules can be complex, particularly for companies with numerous assets. This is where leveraging CMMS (Computerized Maintenance Management System) software becomes indispensable. Not only does it streamline maintenance procedures, it also boosts productivity and provides invaluable insights into machinery conditions.
Understanding the Impact of CMMS Software
Implementing CMMS software revolutionizes maintenance processes by automating and digitizing operations. Beyond scheduling work orders, this advanced technology centralizes asset information, facilitates maintenance report generation and analysis, and empowers data-driven decision-making. With CMMS, businesses can meticulously plan, execute, and adapt maintenance strategies to prevent machine failures and minimize downtime.
Advantages of CMMS in Preventive Maintenance
Transitioning from reactive to preventive maintenance yields numerous benefits, including reduced downtime, enhanced safety standards, prolonged equipment lifespan, and decreased maintenance costs. However, effective preventive maintenance requires the right tools, which CMMS software seamlessly provides.
-
Proactive Maintenance Planning: With CMMS, teams can proactively identify issues and take preventive measures to avoid breakdowns. This helps to ensure that assets are reliable and have a long lifespan, ultimately saving time and money in the long run.
-
Centralized Asset Management: CMMS centralizes all asset-related information into one easy-to-use system, including extensive maintenance histories and detailed inspection logs. This allows organizations to closely monitor their assets' performance, detect and identify trends, and develop strategic asset management plans.
-
Streamlined Work Orders: By leveraging a Computerized Maintenance Management System (CMMS), maintenance teams can streamline their work order processes and improve maintenance efficiency. Automated work orders allow maintenance tasks to be scheduled and assigned automatically, ensuring timely execution and reducing the risk of missing critical routines.
-
Inventory Oversight: With its advanced features, the CMMS can efficiently monitor the availability and consumption of parts and supplies required for routine maintenance tasks. It can also issue timely replenishment alerts to prevent delays and optimize inventory management.
-
In-Depth Performance Analytics: CMMS provides real-time metrics and detailed reports that enable businesses to analyze data closely and optimize maintenance agendas for enhanced performance and cost-effective asset management. By using CMMS, companies can obtain comprehensive insights into their maintenance operations, monitor equipment performance, track maintenance costs, and identify areas for improvement.
-
Regulatory Compliance and Documentation: By facilitating documentation of maintenance actions, CMMS helps organizations meet legal and industry standards. It also helps organizations maintain accurate records of activities, making it easier to identify trends, anticipate issues, and plan for future maintenance activities.
In today's competitive business landscape, preventive maintenance is indispensable for operational success. By integrating CMMS software into workflows, businesses can establish a robust preventive maintenance culture, maintain peak asset performance, extend equipment lifespans, and ultimately increase profitability. For companies that have not yet explored the potential of CMMS software, this is the perfect time to do so, taking advantage of its transformative power and optimizing preventive maintenance strategies for better operational efficiency.